
Have you noticed how automation technologies have made processing raw materials more predictable? Yet, you still face challenges like scarce resources, rising energy costs, staff shortages, and increasingly rigorous regulatory requirements. Digitalization opens new opportunities for you to tackle these challenges and boost productivity and reliability. Imagine a plant where smart manufacturing enhances visibility, streamlines operations, minimizes friction, and reduces costs. As a company with many years of experience in process automation, Endress+Hauser is your reliable partner for improving processes and seizing the opportunities offered by digitalization.
Currently industrial companies are investing: The market research and consulting company InsightAce Analytic has estimated the market size of smart manufacturing at $ 106.75 Bn (in 2023) and forecasts a compound annual growth rate of 16.3 % for the coming years.

Unlocking productivity with smart manufacturing
Smart manufacturing is well-known in factory automation. But what is smart manufacturing in process automation? Industrial processes remain chemical, mechanical, and physical. However, the same principles apply for factory automation and process automation. What makes both worlds smart is the intelligence of the environment. A plant where digital communication goes down to the field level empowers your staff to gain insights, streamline documentation and make data-driven decisions. In a digitally connected facility with interoperable systems, it is easier to increase productivity, adapt to changing demands, meet standards, and make the whole business scalable.
The smart manufacturing principles of the process industry include gaining data insights from the Industrial Internet of Things (IIoT) via connected sensors, implementing remote monitoring and interoperable equipment, visualizing assets through digital twins, and using Artificial Intelligence (AI) for more reliability and predictive applications. After setting up a connected plant as a first step, the use of predictive technologies - e.g. predictive maintenance applications - represents the next level of digital maturity. It makes the plant more reliable and your business more scalable. However, the ultimate goal is to achieve an adaptive plant. By responding to changing trends thanks to data insights and flexible control methods, you safeguard your future business.

Enhancing operational efficiency
How can smart manufacturing principles make a process more efficient? Discover the top five ways to boost your plant's efficiency with smart manufacturing principles:
- Real-time tracking makes data available that facilitates decision-making.
- Digital monitoring helps to avoid human error and manage hazards.
- Digital documentation saves staff time.
- Remote monitoring enables quick (re-)actions.
- Data analysis provides the basis for scaling the business.

Ethernet-based communication
What is needed to apply smart manufacturing principles? Build your digitalization vision on Ethernet-based communication, ensuring your operations are fast and seamless. While EtherNet/IP, PROFINET or Modbus TCP are well known at the control level, many plants still use analog signals or fieldbuses on the shop floor. However, Ethernet technologies are undergoing an exciting evolution in the field. It is now possible to improve the connection between field and control levels, or even to bring Ethernet directly into the field. This is a great way to unlock smart manufacturing principles, leading to easy data access, fast and connected networks, and opening the door for IIoT capabilities.
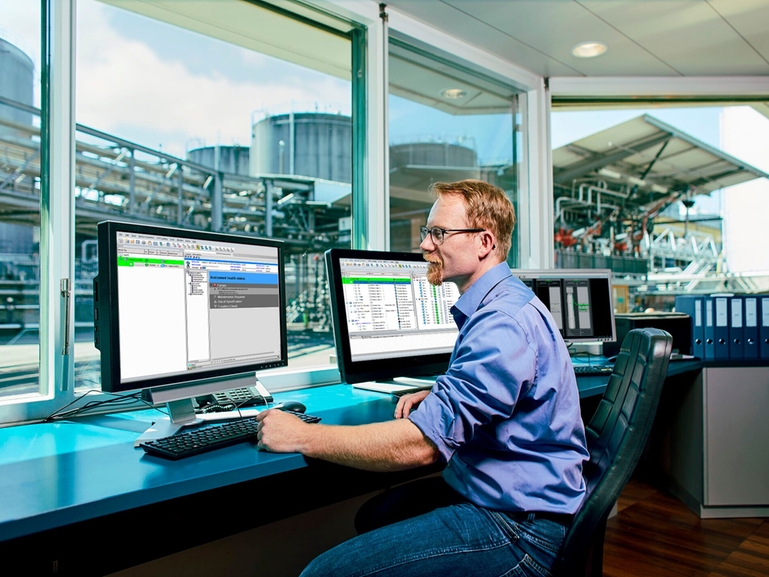
IIoT and AI
To create intelligent and interconnected plants where you can easily access data, make predictions, make decisions, and boost output, you need IoT sensors that can make reliable information remotely accessible. Today, you can retrofit field devices and transform them into IoT sensors. Endress+Hauser offers a variety of edge computing solutions that bridge the physical and digital world. The next level of smart manufacturing is the use of Artificial Intelligence (AI), which can eventually take automated processes to a higher level of autonomy.